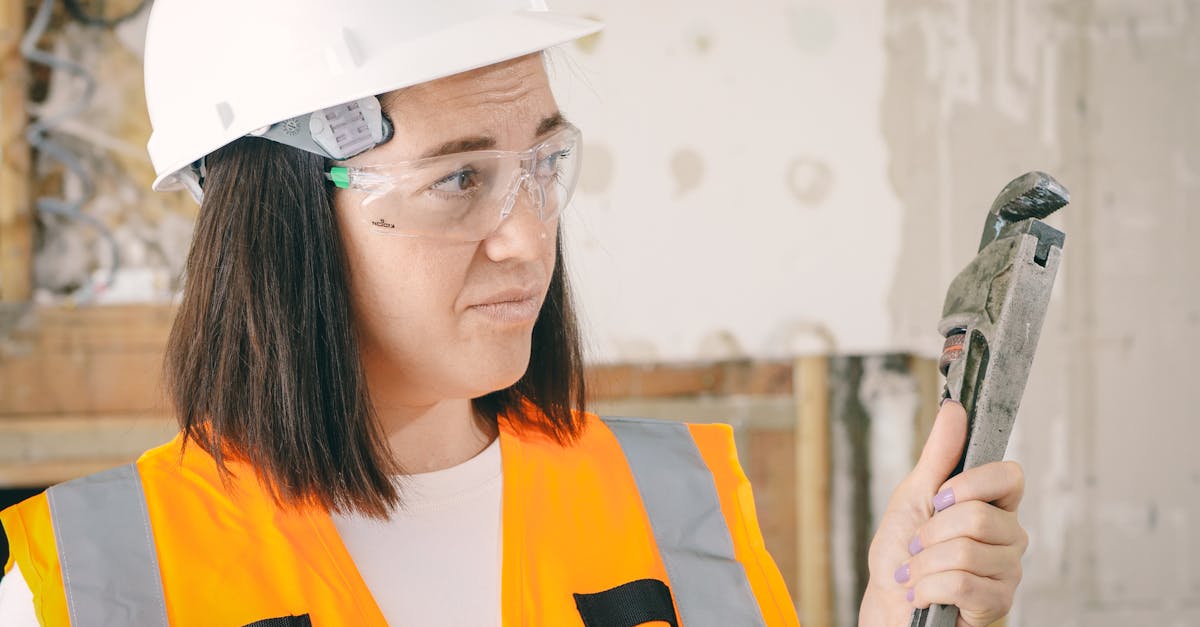
Table Of Contents
Documenting NonCompliance Reports
Proper documentation is crucial when reporting non-compliance in pipe installation and repair. Detailed records provide a clear account of observed issues, dates of incidents, and any communication that has occurred with relevant parties. This information should be gathered as soon as possible to ensure accuracy. Photographic evidence, sketches, and witness statements can further substantiate claims of non-compliance. Organising these details in a comprehensive format enhances the report’s clarity and effectiveness.
In addition to documenting the incidents themselves, it is important to outline any specific regulatory guidelines or industry standards that have been breached. This context not only supports the validity of the report but also highlights the significance of adhering to these regulations in pipe installation and repair. When creating documentation, consider utilising standard reporting templates that capture all necessary information. Doing so promotes consistency and improves the chances of a timely and effective response from the relevant authorities.
Essential Information to Include
When documenting a non-compliance report related to pipe installation and repair, it is crucial to gather comprehensive details that accurately reflect the issue at hand. Identifying the specific location, including site addresses and relevant plans or diagrams, will provide context for the non-compliance. Clearly noting the date and time of the observation, as well as the individuals involved in the installation or repair, adds to the report's credibility. Photographic evidence can serve as a powerful tool to support claims, so including clear images that illustrate the non-compliance helps substantiate the findings.
In addition to basic details, it's essential to describe the nature of the non-compliance in a factual manner. This should include the type of pipe used, any deviations from approved specifications, and potential impacts on safety or serviceability. If applicable, reference specific legislation or industry standards that were not met during the process. Providing a summary of previous communications or attempts at resolution, if any, can also demonstrate a proactive approach to addressing the non-compliance. Such thorough documentation will enhance the effectiveness of the report and aid in the resolution process.
Following Up After Reporting
After submitting a non-compliance report, it is crucial to establish a systematic approach for following up. Monitoring the progress of the report ensures that necessary actions are taken to address the identified issues. Maintaining clear communication with relevant parties involved in pipe installation and repair can facilitate timely responses and help prevent further complications. Regular updates on the status of the report can also enhance trust and encourage a culture of accountability.
Ensuring accountability and transparency is essential for effective follow-up. Stakeholders should be kept informed about the steps being undertaken to rectify non-compliance issues. This not only reinforces the importance of adherence to standards in pipe installation and repair but also encourages a proactive attitude towards compliance. Clear documentation of interactions and actions taken post-report can provide valuable insights for future improvements and help foster an environment that prioritises safety and regulatory adherence.
Ensuring Accountability and Transparency
Ensuring accountability and transparency in non-compliance reporting is crucial for maintaining safety and quality standards in pipe installation and repair. Clear communication between workers, supervisors, and stakeholders helps create a culture of responsibility. When parties are encouraged to share concerns without fear of retribution, it fosters an environment where issues can be addressed promptly and effectively. Proper documentation of non-compliance also plays a significant role in tracking recurrent problems and identifying areas that require improvement.
Regularly reviewing and addressing reported non-compliance incidents promotes a stronger oversight mechanism. Engaging all team members in discussions about the importance of adherence to regulations and standards enhances collective awareness. This practice not only helps in rectifying ongoing issues but also mitigates future risks associated with pipe installation and repair. By establishing transparent procedures for handling non-compliance reports, organisations can bolster trust among employees and regulatory bodies alike, ultimately leading to better compliance outcomes.
Legal Implications of NonCompliance
Non-compliance in pipe installation and repair can lead to serious legal ramifications. Regulatory bodies enforce strict adherence to guidelines that govern the industry, and failure to meet these standards can result in significant penalties. Companies may face hefty fines, suspension of operations, or even legal action from affected parties. In some cases, non-compliance can result in civil lawsuits if defects lead to property damage or personal injury, making it crucial for organisations to understand their obligations.
Understanding the regulatory frameworks surrounding pipe installation and repair is essential for ensuring compliance. These frameworks often differ by state and territory, necessitating thorough awareness of local laws and requirements. Regular training and audits can help mitigate risks by ensuring that all personnel are informed about current regulations. Maintaining meticulous records of compliance efforts can also serve as a protective measure in the event of an investigation or dispute, highlighting a proactive approach to adhering to statutory requirements.
Understanding Regulatory Frameworks
Understanding the regulatory frameworks surrounding pipe installation and repair is essential for ensuring compliance and safety. Various Australian standards and codes outline the requirements for materials, installation methods, and maintenance practices. Familiarity with these regulations helps organisations avoid costly penalties and enhance the overall integrity of their projects. It also provides a guideline for best practices, ensuring that all activities meet the specified safety and quality benchmarks.
Each state and territory may have its own set of rules governing pipe installation and repair, which adds complexity to compliance efforts. Stakeholders must stay informed about local regulations as well as national standards. Engaging with industry bodies and regulatory agencies can provide valuable insights into current requirements. This proactive approach not only facilitates adherence to the law but also fosters a culture of safety and responsibility within the workforce.
FAQS
What should be included in a non-compliance report for pipe installation?
A non-compliance report should include essential information such as the specific non-compliance issue, location details, date and time of occurrence, involved parties, and any relevant photographic evidence or documentation.
How can I ensure accountability after reporting non-compliance in pipe installation?
To ensure accountability, you should document all communications related to the report, follow up with the appropriate authorities or management, and keep a record of any actions taken in response to the report.
Are there legal ramifications for non-compliance in pipe installation?
Yes, non-compliance in pipe installation can lead to legal ramifications, including fines, penalties, or even legal action taken against individuals or companies responsible for the non-compliant work, depending on the severity and regulatory framework involved.
What regulatory frameworks should I be aware of when reporting non-compliance?
It's important to understand local, state, and national regulations that govern pipe installation, as they can vary greatly. Familiarise yourself with standards set by organisations such as the Australian Standards (AS) and relevant state-based regulatory bodies.
How can I report non-compliance anonymously?
Many organisations have established whistleblower protection policies or anonymous reporting channels. You can inquire about these options within your organisation or reach out to regulatory bodies that may allow anonymous submissions of non-compliance reports.