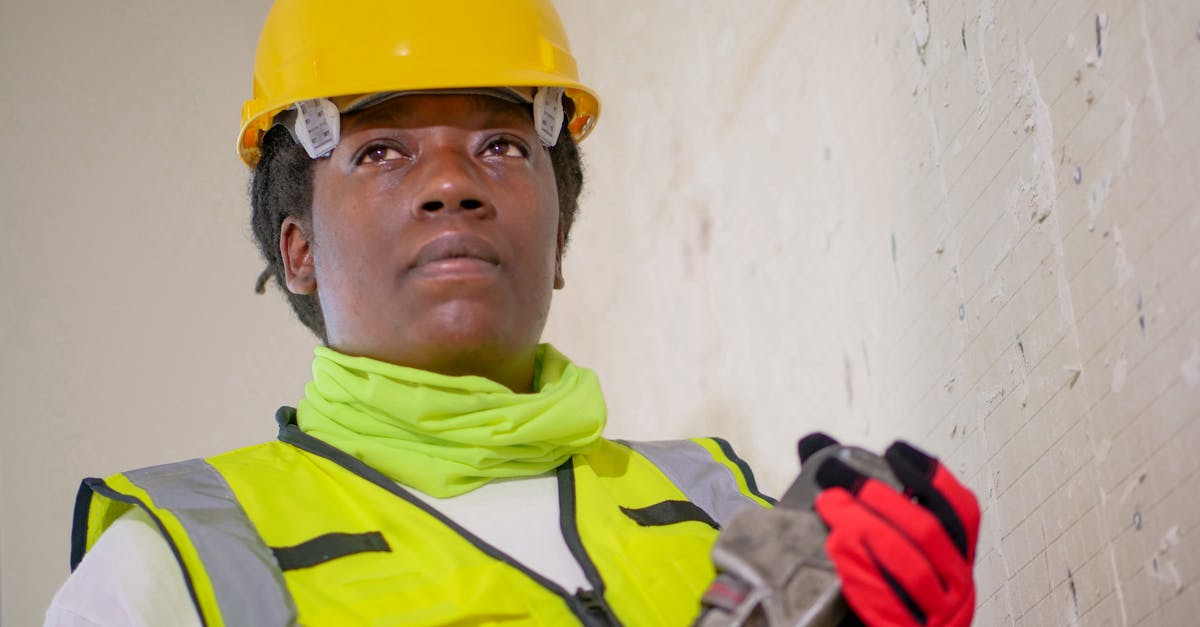
Table Of Contents
Tools and Equipment Safety
The safety of tools and equipment used in pipe installation and repair is paramount. Workers must be equipped with the correct tools for the task to avoid accidents and ensure efficiency. Regular inspection of tools and equipment is essential to check for wear and tear or malfunction. Any damaged items should be reported immediately and replaced or repaired before further use. Proper storage after use also helps in maintaining tool integrity and optimising their lifespan.
Training on the safe use of equipment is a critical aspect of workplace safety. Workers should receive comprehensive instruction on operating tools correctly, including understanding the specific functions and potential hazards. Adhering to safety guidelines will minimise the risk of injury during pipe installation and repair activities. Having a designated safety officer or supervisor on-site can further enhance adherence to these protocols, ensuring that safety remains a top priority throughout the project.
Ensuring Proper Use and Maintenance
Proper use and maintenance of tools and equipment is essential in ensuring safety during pipe installation and repair works. Workers should be trained to handle equipment according to manufacturer guidelines. Regular inspection of tools for any signs of wear and tear helps in identifying potential hazards before they result in accidents or injuries. Keeping a maintenance log for each piece of equipment can support timely servicing and replacements, which is crucial in maintaining optimal performance.
Furthermore, all equipment should be stored securely when not in use. This prevents unauthorised access and reduces the risk of damage. Employees should be encouraged to report any malfunctions immediately. Creating a culture of safety requires ongoing education regarding the importance of using tools correctly. Reinforcing these practices not only enhances safety but also improves efficiency during pipe installation and repair tasks.
Worksite Safety Assessments
A thorough worksite safety assessment is essential for any pipe installation and repair project. Identifying potential hazards allows teams to implement necessary precautions before work commences. This process involves reviewing the site layout, evaluating existing infrastructure, and considering environmental factors that may impact operations. Workers should be familiar with the specific risks associated with the location, including underground utilities, traffic flow, and weather conditions.
Regular safety inspections contribute significantly to maintaining a safe worksite. These checks should be conducted before and during pipe installation and repair activities. Inspectors should look for clear access routes, proper signage, and the correct placement of equipment. Ensuring that all safety protocols are strictly followed can mitigate risks and promote a culture of safety among team members.
Conducting Effective Safety Inspections
Effective safety inspections are critical in ensuring a secure environment during pipe installation and repair. These inspections should be carried out before work commences, focusing on identifying potential hazards like leaks, exposed wires, or unstable structures. Each inspection must involve a thorough assessment of the tools and equipment to confirm they meet safety standards and are in good working condition. Proper documentation of the findings is essential, as this provides a reference for future inspections and highlights areas that may require attention.
Regularly scheduled safety inspections foster a culture of safety among team members engaged in pipe installation and repair tasks. It is vital to engage workers in the process, encouraging them to voice concerns and report unsafe conditions. This proactive approach not only enhances the overall safety of the worksite but also cultivates a sense of responsibility among staff. By addressing issues promptly, the likelihood of accidents or injuries can be significantly reduced, promoting both worker wellbeing and project efficiency.
Implementing Lockout/Tagout Protocols
Lockout/Tagout (LOTO) protocols are essential in maintaining safety during pipe installation and repair operations. These procedures ensure that all energy sources are effectively isolated before any work begins. Workers must familiarise themselves with the specific energy control procedures relevant to their tasks. Proper training should be provided to all personnel involved, emphasising the importance of locking out machinery and tagging it to communicate that maintenance is underway.
To implement LOTO effectively, a robust system should be in place that includes clear guidelines for locking out equipment. Each team member needs access to the necessary locks and tags, and they should consistently follow the established procedures. Conducting regular training sessions reinforces the importance of these protocols, ensuring that every worker understands how to prevent accidental equipment activation. Ultimately, stringent adherence to Lockout/Tagout protocols contributes significantly to a safer work environment during pipe installation and repair activities.
Preventing Accidental Equipment Activation
Preventing accidental equipment activation during pipe installation and repair is critical for maintaining a safe work environment. Clear communication among team members is essential. Regular safety briefings can ensure everyone understands the protocols in place. This involves identifying all potential hazards associated with equipment operation. Keeping the area tidy also minimises distractions that could lead to inadvertent actions.
Implementing lockout/tagout procedures is a fundamental practice to prevent machinery from being energised. Before commencing work on any equipment, it should be properly shut down and tagged out. This action prohibits unauthorized use and reinforces the safety measures in place. Additionally, training workers to recognise the importance of these protocols fosters a culture of safety that significantly reduces risk during pipe installation and repair operations.
FAQS
What are the essential tools and equipment needed for pipe repair works?
Essential tools for pipe repair include pipe wrenches, screwdrivers, pliers, pipe cutters, welding equipment, and safety gear such as gloves, goggles, and hard hats.
How can I ensure proper use and maintenance of tools and equipment?
Proper use and maintenance can be ensured by regularly inspecting tools for wear and tear, following manufacturer instructions, cleaning after use, and storing them in a designated area.
What should I include in a worksite safety assessment?
A worksite safety assessment should include identifying potential hazards, evaluating the risks associated with those hazards, ensuring proper signage is in place, and checking that safety equipment is readily available.
How often should safety inspections be conducted on a worksite?
Safety inspections should be conducted regularly, ideally before each shift, and also when there are significant changes in the work environment or after any incidents.
What are Lockout/Tagout protocols and why are they important?
Lockout/Tagout protocols are safety procedures used to ensure that hazardous machinery is properly shut off and not able to be started up again before maintenance or repair work is completed. They are important to prevent accidental equipment activation, protecting workers from potential injuries.